
Failures could also be generated in the HAZ due to the gradient of the coefficient of thermal expansion that would increase the residual stresses at specific points. Dissimilar joints are designed based on system requirements, since some irregularities can occur, such as the unmixed zone (laminar layer of base metal which has melted and resolidified in situ during the welding process) between the electrode and the base materials due to the variation in chemical composition, diffusion of alloying elements that can generate an increase or loss of hardness in the interface between the bead of weld and the base material, or a non-homogeneous microstructure in the weld bead that can generate cracking due to the mixture of two different alloys. However, the mechanical strength for the dissimilar joint must be characterized for proper design and safety requirements. Due to their great versatility, dissimilar welds are applied in the chemical, nuclear, petrochemical, aeronautical, and automotive industries, where it is possible to weld metallic materials such as pipes, profiles, plates, and sheets of different chemical compositions. The joint between different materials has drawn attention in recent years, since they have a good cost–safety ratio. Systems in operation may sometimes present different working conditions that need to be designed under critical operating conditions however, non-critical operating areas can be redesigned using lower cost materials, while maintaining the safety of the system. Finally, dissimilar welding subjected to tensile test failed in the low carbon steel (270 MPa), out of the heat affect zone, thus a good dissimilar joint between both steels was obtained. During impact tests, the absorbed energies were 19.3, 50.7, and 50.2 J for low carbon, dual phase steel, and the welded dissimilar joint respectively. The variation in microhardness profile was produced by the presence of different phases, and the temperature at the end of dual phase heat affect zone was approximately 242 ☌. The welding heat input generated martensite and grain growth in the dual phase heat affect zone, while grain growth and perlite phase increased in the low carbon heat affected zone. Weld thermal cycles were obtained by means of K type thermocouples. The tensile strength was 540 and 275 MPa in dual phase and low carbon, respectively.
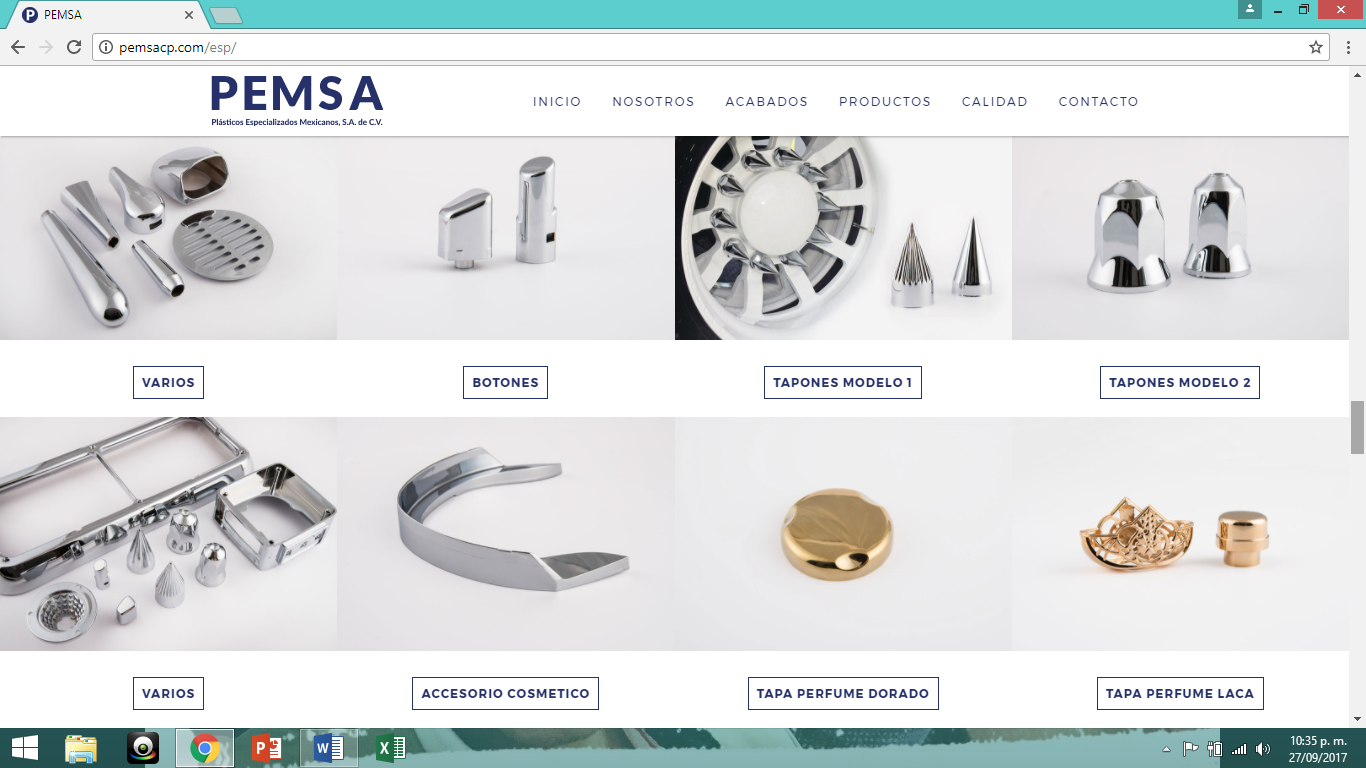
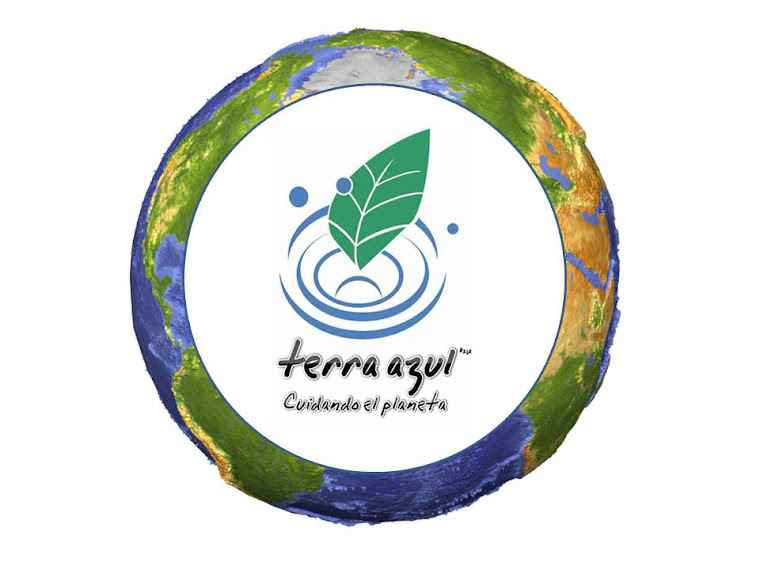
Microhardness profile, tensile, and impact tests were used to evaluate the mechanical behavior, while optical and scanning electron microscopy were employed to evaluate the microstructural changes. The focus of this work is to study the microstructural–mechanical properties of dissimilar welding DPC340Y590T dual phase–JSC270C low carbon steels. Dissimilar welding used in the automotive area are possible joints with the GMAW process however, its structural performance must be evaluated.
